品質管理
Quality Control 品質管理
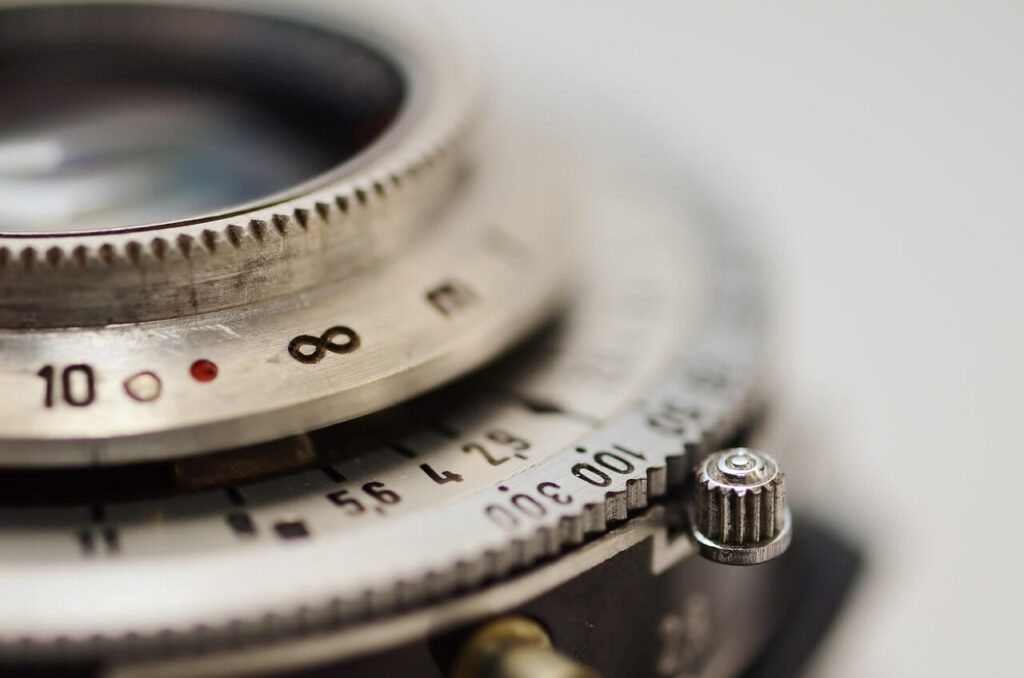
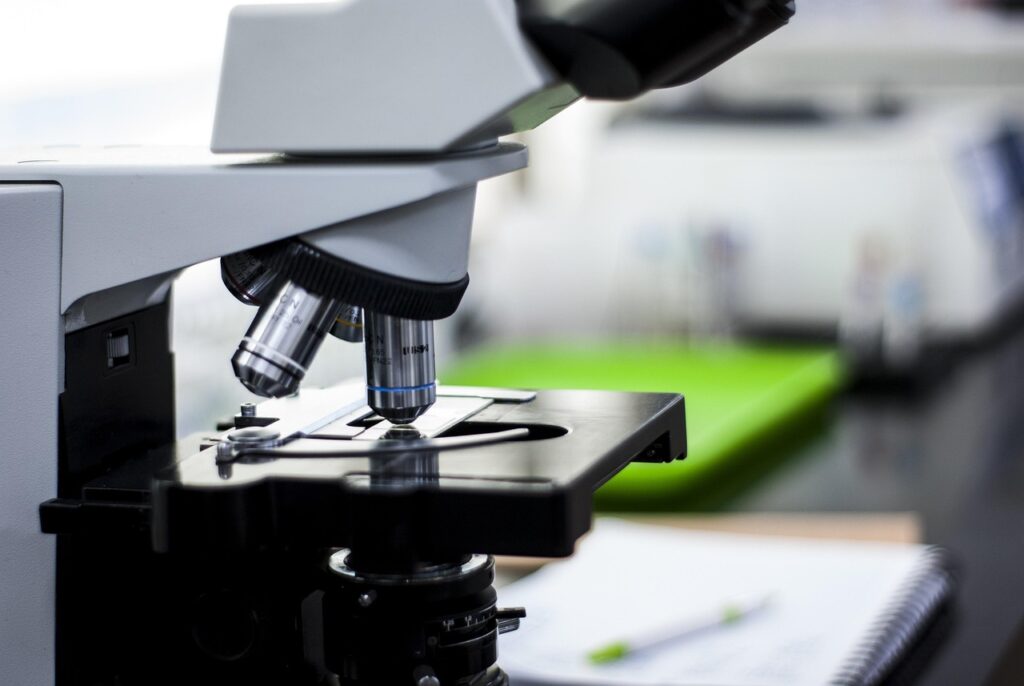

品質方針
1.我々は、常に顧客に満足していただける製品を追求することを通じ、広く社会に貢献し、ともに成長し、歩み続けます。
2.我々は、自らの仕事に誇りを持ち、人それぞれの能力を十分に発揮できる職場を築き上げます。
3.我々は、現状に満足することなく、常に技術と品質の向上に全力を注ぎます。
品質検査の基準
綿密な加工プランに基づき生産に努め、異常を発見したなら即対処、現場の生産管理を徹底しています。
目的: 加工材料の品質を初期段階で確保し、不良品の混入を防ぐ。
実施内容:
入庫材料について外観検査、寸法測定、成分分析などを実施。
各材料が指定された基準値を満たしているか確認。
検査結果をデータベースや台帳に登録し、履歴を管理。
不良品や疑わしい材料は隔離し、サプライヤーに連絡して対応を協議。
目的: 材料の状態を明確化し、品質管理を徹底する。
実施内容:
合格品には「検査済み」ラベルを貼付し、使用可能な領域に保管。
不良品には「不良品」ラベルを貼付し、隔離保管、廃棄または返品手続きを開始。
未検査品には「検査待ち」ラベルを貼付し、専用の保管エリアに移動。
ラベルには検査日、ロット番号、品名などを記載しトレーサビリティを確保。
目的: 最終製品が顧客要求仕様を満たすことを保証。
実施内容:
検査項目:寸法検査、外観検査、機能性試験、部品の耐久試験など。
検査基準を顧客の仕様に基づき設定。
専任検査員がチェックリストに基づき検査を実施。
検査記録を残し、合格品には出荷許可を与える。不合格製品は原因調査を行い、必要に応じて再加工または廃棄。
目的: 検査結果の信頼性を保持するため、機器の精度を維持する。
実施内容:
定期的な校正スケジュールを設定し、据え付け状態や精度の確認を実施。
日常的に使用前後に簡易点検を行い、異常があれば修理または交換。
校正作業における記録や証明書を保管。
校正期限切れの機器は使用停止し、適切な機器と交換。
目的: 生産中の異常を早期に発見し、問題を未然に防ぐ。
実施内容:
巡回検査タイミング:始業時と中間時の2回。
検査範囲:作業員の手順、設備の稼働状況、製品状態、作業環境など。
専用チェックシートを使用し、異常が発生した場合は詳細に記録。
異常発見時は現場で仮対策を講じ、詳細調査後に恒久対策を実施。
重大な問題については管理者へ即時報告し、対応を指示。
目的: 顧客満足度を維持し、企業としての信頼性を確保。
実施内容:
顧客からの品質に関するクレームは即時受け取り、担当部署に連絡。
関係する製品ロットのトレーサビリティを使用して原因を迅速に追究。
問題の原因が明確になれば、改善策を設計し、再発防止の対策を講じる。
改善作業の進捗を顧客に定期的に報告し、信頼回復を図る。
改善後のプロセスや仕様変更は社内全体に共有し、品質を底上げ
品質管理検査
加工現場での検査はもちろんのこと、専用検査室での最終検査でも厳しいチェックをしております。常にお客様に信頼される製品造りを行い、納得頂ける製品をご提供いたします。
-768x1024.jpeg)
-2-1024x768.jpeg)
-1-1024x768.jpeg)
.jpeg)
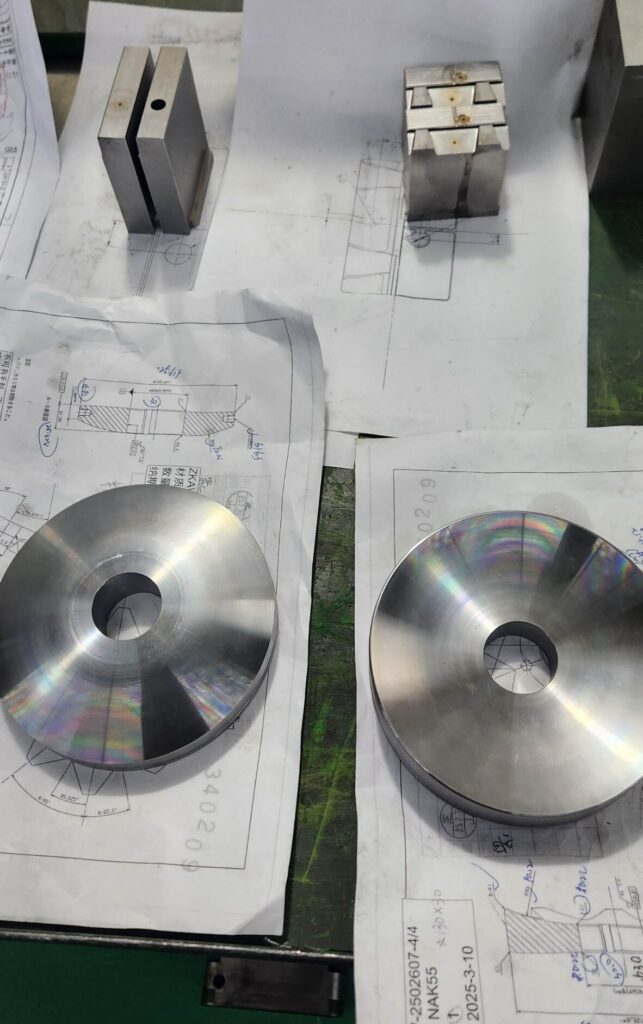
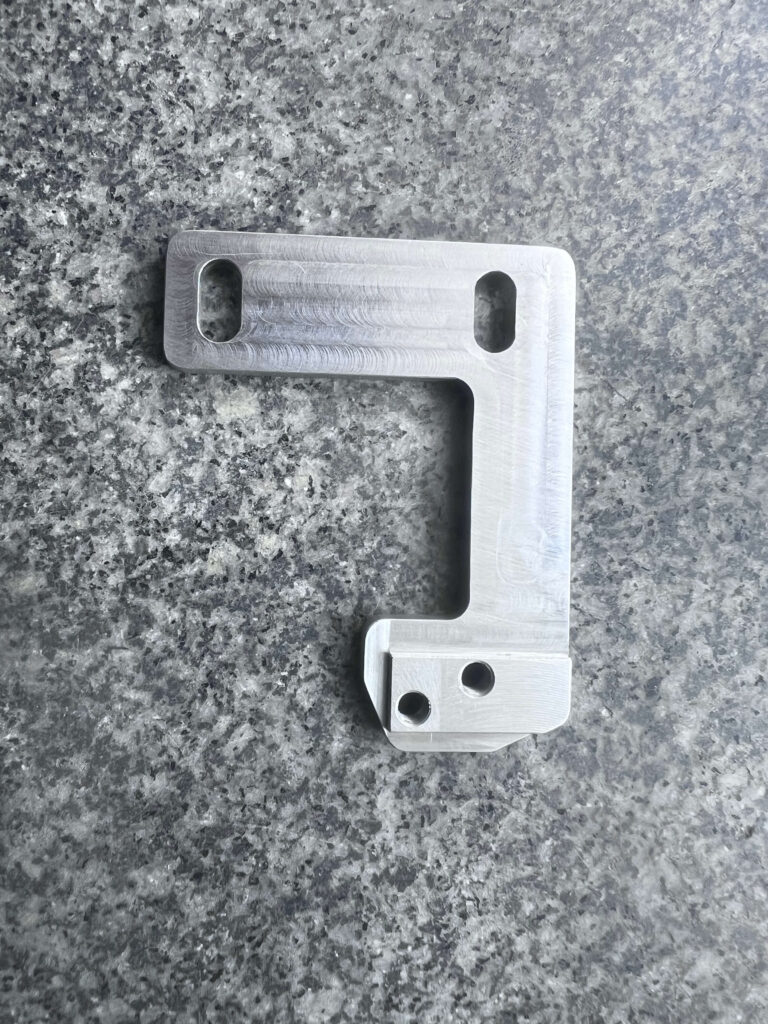